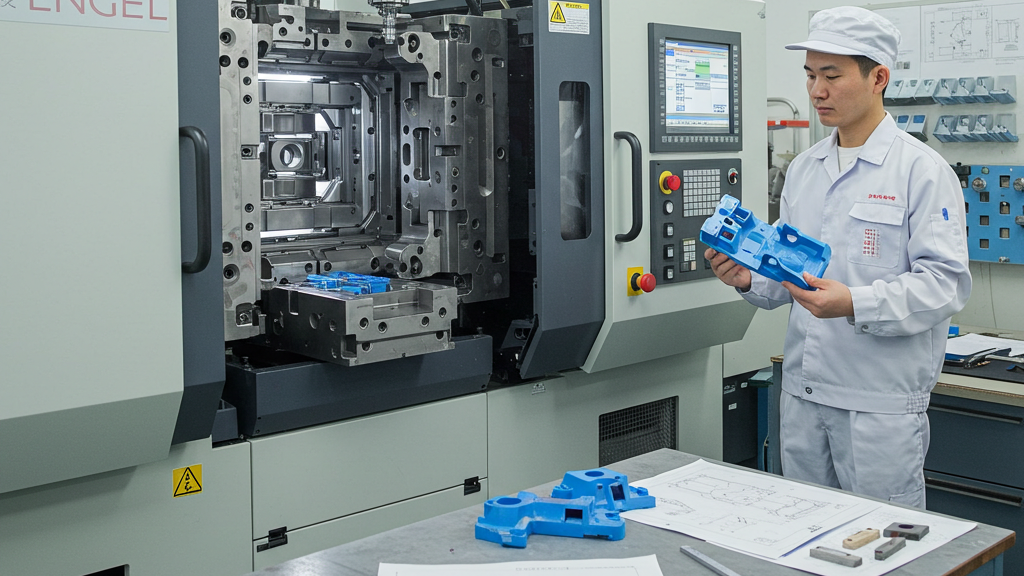
Demolding is a critical step in the production of ABS injection molded parts. Improper demolding operations can easily lead to product defects and affect production efficiency. Mastering the correct demolding techniques can effectively improve product quality.
The demolding of ABS injection molded parts is influenced by various factors, including mold design and process parameters. Reasonable mold design can reduce demolding resistance, while optimizing injection molding process parameters can also significantly improve demolding effectiveness.
How Do the Properties of ABS Materials Affect Demolding of Injection Molded Parts?
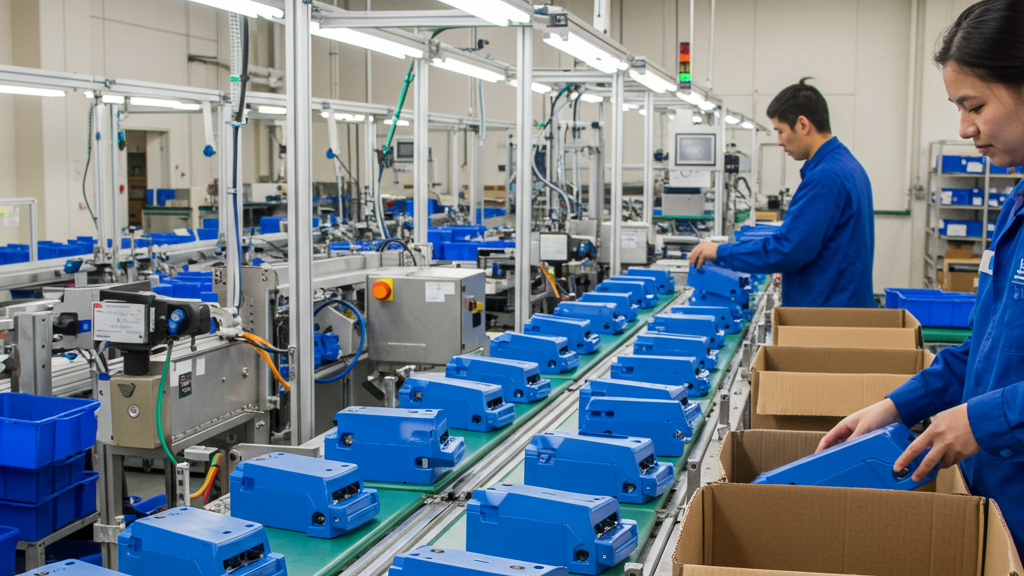
Understanding key properties of ABS materials, such as shrinkage rate, adhesion, and thermal expansion coefficient, is fundamental to optimizing the demolding process and reducing product defects. An in-depth analysis of how these properties interact with the mold is crucial for improving demolding effectiveness.
- Shrinkage Rate: The shrinkage characteristics of ABS materials cause the molded part to tightly grip the core, increasing demolding difficulty.
- Adhesion: ABS materials tend to adhere to molds at high temperatures, necessitating optimization of mold surface treatments and temperature control.
- Thermal Expansion Coefficient: ABS materials have a high thermal expansion coefficient, and dimensional changes due to temperature fluctuations must be considered during demolding.
- Melt Viscosity: The high melt viscosity of ABS can lead to mold sticking under high-pressure injection, requiring precise control of injection pressure and speed.
Which Aspects of Mold Design Are Critical for Demolding ABS Injection Molded Parts?
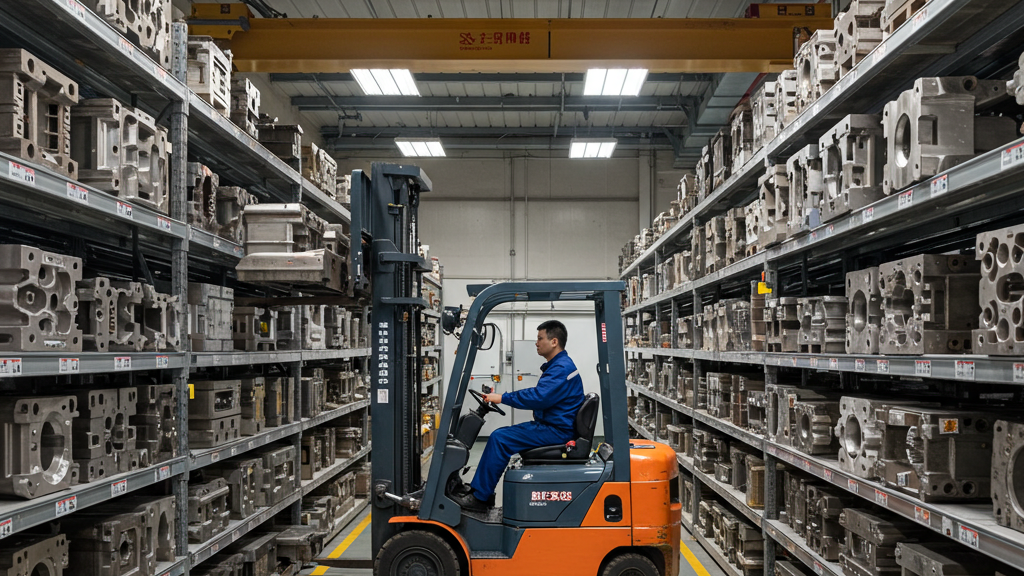
From draft angles to the design of the ejection system, every detail can significantly impact the demolding of ABS injection molded parts. A thorough understanding of these design elements is key to optimizing the demolding process and avoiding product defects.
- Draft Angles: Sufficient draft angles are essential to ensure smooth demolding of ABS parts.
- Ejection System: A well-designed ejection system helps prevent deformation and damage during demolding.
- Mold Surface Treatment: A smooth mold surface reduces the adhesion of ABS material, lowering demolding resistance.
- Mold Cooling System:An even cooling system minimizes the deformation of ABS parts and improves dimensional stability.
How to Optimize to Improve the Demolding Effect of ABS Injection Molded Parts?
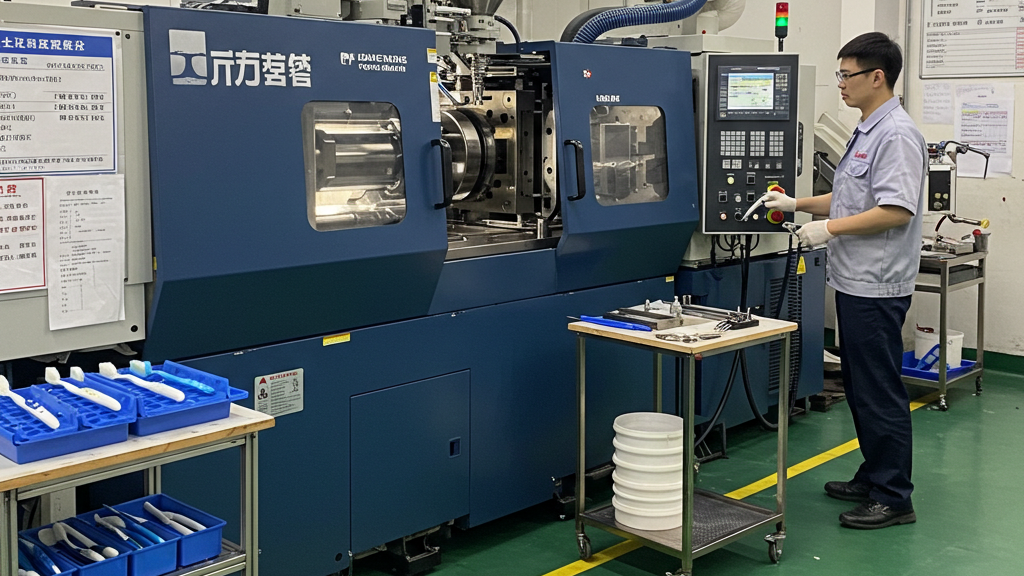
Optimizing injection molding process parameters is key to improving the demolding effect of ABS injection molded parts. By precisely controlling temperature, pressure, and speed, demolding resistance can be effectively reduced, enhancing product quality and production efficiency.
- Temperature Control: Accurately control the melt and mold temperatures to ensure ABS material fluidity and minimize deformation.
- Pressure Control: Adjust the injection and holding pressure appropriately to avoid excessive pressure that increases demolding resistance.
- Speed Control: Maintain suitable injection and demolding speeds to ensure uniform filling and reduce impact damage.
- Cooling Time: Ensure sufficient cooling and solidification to minimize demolding deformation while balancing production efficiency.
Stripping method and effect evaluation of ABS injection parts
Auxiliary Demolding Methods | Applicable Scenarios | Advantages | Disadvantages | Effect Evaluation |
Mold Release Agent Spraying | Complex Structures, Deep Cavity Molds | Reduces Sticking, Improves Efficiency | May Affect Secondary Processing | Significantly Improves Demolding, Reduces Product Defects |
Vacuum-Assisted Demolding | Thin-Walled, Easily Deformed Products | Reduces Demolding Force, Reduces Deformation | Higher Equipment Costs | Suitable for Precision Products, Improves Dimensional Accuracy |
Compressed Air-Assisted Demolding | Small, Complex Structures | Cleans Molds, Assists Demolding | May Produce Noise | Suitable for Small Parts, Improves Demolding Speed |
Vibration-Assisted Demolding | Severe Sticking, Complex Structures | Reduces Friction, Assists Demolding | May Produce Noise | Suitable for Severe Sticking, Improves Demolding Success Rate |
Improving the Demolding Success Rate of ABS Injection Molded Parts through Process Enhancement
Demolding is a critical step that directly affects product quality and production efficiency. By optimizing the injection molding process, we can significantly improve demolding success rates, reduce product defects, and lower production costs.
1.Temperature Control: Accurately control the melt and mold temperatures to ensure ABS material fluidity and minimize deformation.
2.Pressure Control: Adjust the injection and holding pressure appropriately to avoid excessive pressure that increases demolding resistance.
3.Speed Control: Maintain suitable injection and demolding speeds to ensure uniform filling and reduce impact damage.
4.Cooling Time: Ensure sufficient cooling and solidification to minimize demolding deformation while balancing production efficiency.
Conclusion
By considering these factors and making adjustments based on actual production conditions, the demolding effect of ABS injection molded parts can be improved, enhancing product quality and production efficiency.
For expert assistance in implementing for your production needs, visit our resource center or contact us. Let’s help you scale up your manufacturing with precision and efficiency!
Post time: Mar-21-2025